In conversation with Maurice Ditewig, Director Industrial Automation at Hellebrekers
4 February 2021
Advanced manufacturing technologies are transforming all parts of industry and many of the European companies at the forefront of that transformation are SMEs. In this latest edition of our ‘In conversation with’ series, we sat down with Maurice Ditewig, Director of Industrial Automation at one such company, Hellebrekers, to talk about what advanced manufacturing looks like from his perspective, where the opportunities lie and how to seize them. Hellebrekers is a member of FME, the Dutch employers' organisation for the technology industry, which is a member of Orgalim.
You will also be able to hear from Maurice Ditewig at our upcoming event on Global Technology Leadership in Action, so please join us there!
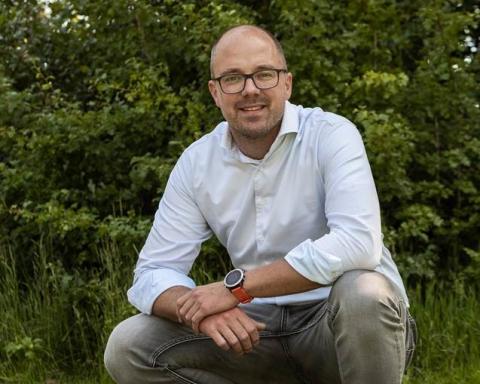
Hellebrekers has been in business for 50 years this year. How did you get into industrial automation?
Hellebrekers has been busy with commercial swimming pool installation activities, as you say, for 50 years now. It was from the perspective of building automation that we grew slowly into the industrial automation side. So in the last 30 years, we have grown from a local installation company in the Veluwe, Netherlands, to an international systems integrator. About 80 of the company’s 250 employees now work in the industrial automation business, which I lead. We design, develop and integrate software and hardware tools to optimise production processes for a wide range of clients in the manufacturing and process industries.
What does ‘advanced manufacturing’ mean to you?
Advanced manufacturing for me and for our team is part of the whole Industry 4.0 movement and taking us towards Industry 5.0. There are a lot of new techniques that are out there already and they're affordable, but they're not really being deployed yet. Advanced manufacturing starts with using these available techniques, because they can really help industry become more efficient, more flexible, lower costs and ultimately strengthen its competitive position not only on a company level, but also in Europe and a worldwide.
We talk to a lot of end clients that have been working in the process industry for many years and they're always busy with the day-to-day business, focused on reducing costs and working to increase the quality of the product. So step one is the digitalisation of their production data, because data is key and can be used for new insights: for feeding AI models, for example. The second phase is to start looking at the bottlenecks in the production processes, that may be cost, or personnel availability, or quality losses. For example, a lot of companies are reactive when it comes to problems in the production facility: something happens, then they react. But if you can use the data you collect and put it into an AI module, you can be much more proactive about potential issues and that way minimise downtime and production losses.
The demand for customisation is increasing. To keep up with this pace, we need people to do the creative thinking to design what is demanded. Automation gives people time to focus on more important tasks.
We also still bump into a lot of companies where a lot of manual labour is being done that is dull and heavy, which can be easily automated by robotics. This is important because the demand for customisation is increasing and, to keep up with this pace, we need people to do the creative thinking to design what is demanded. Automation gives people time to focus on more important tasks. This is where we start moving into Industry 5.0.
Can you give us a real-life example?
I can give you two. Kornelis Caps & Closures makes lids and caps for a wide variety of containers. They have more than 35 moulding machines and, in the old factory, all the machines were stand-alone and all information was kept on paper documents and in people's heads. Now they have connected the complete process from office to all the machines to each other and to our Visual Link MES software. The complete process, from order intake through production, has been automated and integrated and it’s now completely paperless. The operators, instead of having to rely on spotting a problem with one of the many machines – usually after it had happened – can now check on things via a tablet and are proactively made aware of any issues, so they can be solved at once.
Another company we work with produces big industrial fittings for pipes, that need to meet very strict quality control standards for their clients. They were concerned that they were relying on basically one skilled person to manually check something like 400,000 units a year. What happens if that person is sick, or leaves? So we developed a cobot – a collaborative robot – and mounted an industrial camera on the end of it that creates images of the inside of each fitting, which are then fed into an algorithm that warns if something looks wrong. The person who is in charge of the quality check now has a whole new dimension to his task: he’s responsible for operating the system but also maintaining it. On the other hand, because the quality check is automated by AI, a wider workforce can do the job.
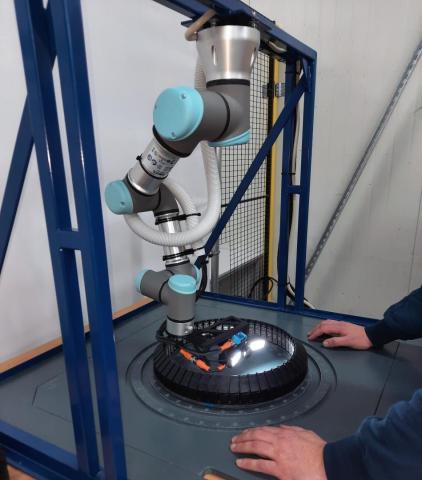
We're very proud of this type of development where a lot of things come together – cobot, vision and AI – and the beautiful part is that while we were developing this particular solution, we used 3D printing techniques to make the custom connection between the camera and the robot. Using 3D printing techniques reduced our production time and that makes us flexible.
What obstacles do you face in helping companies to shift to advanced manufacturing techniques?
The main particular challenge for us is the availability of skills. New techniques are coming through really fast and our challenge is to adapt those techniques and implement them at our customers. But to do that you need engineers who understand and can implement those new techniques. And of course, Hellebrekers is not the only systems integrator in the Netherlands or in Europe and there's a battle going on with everyone trying to attract those engineers. It’s a problem for the whole industry: if you want to position our production facilities so they can compete with the rest of the world, we need engineers.
The other obstacle from my point of view is access to financial support. There's financial aid available to develop new techniques and stay ahead of the global competition in developing the techniques, but we forget more or less to implement them. A lot of companies are willing to implement but they need a bit of a push. The work of the FME really helps, but they still need help closing the business case. So that's why I say the techniques are there, but sometimes we need some starting money to start implementing them.
Small to medium sized enterprises represent 99% of all businesses in the EU. Do you see this as a weakness or a strength for Europe as a whole?
If you look at the number of SMEs out there, similar companies to us, they are Europe's innovation strength. If you combine all the development power, all the integration power, it's a tremendous force that really strengthens our position, really strengthens our innovativeness. Large companies may have more financial resources but they have more moving parts, and they're less flexible.
I believe it is a great strength that Europe has so many small businesses, we just need to find each other and work together more.
So I believe it is a great strength that Europe has so many small businesses, we just need to find each other and work together more. It's a movement that's building: people understand more that you can't win by yourself and that's the strength of Europe. Altogether the speed, at which we develop is tremendous. Europe is smart and we're willing to work together. But that speed needs to be matched in implementing.
We do our best at the micro level but we need to find ways together, maybe on a European level, to speed up the implementation of advanced manufacturing techniques to strengthen our position on the global level. Because there is a lot to gain within current production facilities.